
These approaches also teach that the process must be documented in a manner that allows it to be transferred to other molding machines with the intent of achieving relatively consistent part quality. relative shear rate” curves), as well as methods for establishing an ideal transfer position, ensuring the proper melt temperature, finding the ideal hold pressure, identifying pressure losses within the mold, and finding the time when gate seal (gate freeze) occurs. Among the procedures taught are a method for determining a fill time or fill speed using in-mold rheology curves (a.k.a “relative viscosity vs. These approaches involve similar specific procedures that help establish a foundation on which to build a process. A number of schools, companies, and individuals provide a valuable service to the industry by teaching these structured methods, which have been labeled with terms such as Scientific Molding, Decoupled Molding, and 2-Stage and 3-Stage processes. Tel: 23 Fax: 23.Injection molding process methodologies have evolved over the decades from a seat-of-the-pants black art to a more structured approach. A number of less than 4%/1000 is state of the art. What does this mean? This test measures the machines sensitivity to changes in material viscosity due to all causes, including a change in the material, plastic temperature or mold temperature. Follow the link under Additional Information for the Load Sensitivity Formula. On the same air-shot, record the peak injection pressure on the digital gauge. On this air-shot, record the time it takes from the start of the shot to reach the same stroke position set up in Step 1. (Second stage must be set lower than first-stage peak.
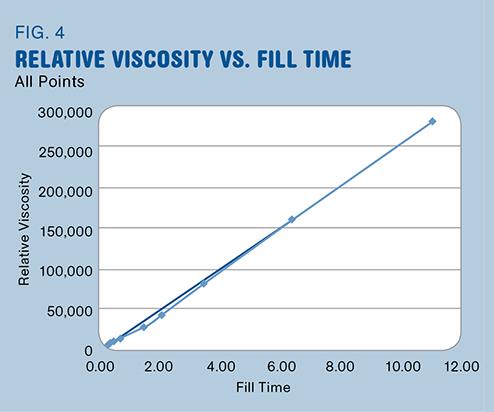
Do not change the stroke transfer position. On cycle, pull back the carriage and purge into the air. (If you want the gauge to hold the peak until manually reset, set SP to a -010 or lower)ĥ. Put the switch in SP and adjust SP knob to about 100. NOTE: To use the digital gauge on the injection cylinder, with switch in TRK, first zero the display to a 000 reading with no pressure. This is the peak pressure it took to reach the transfer cutoff point.
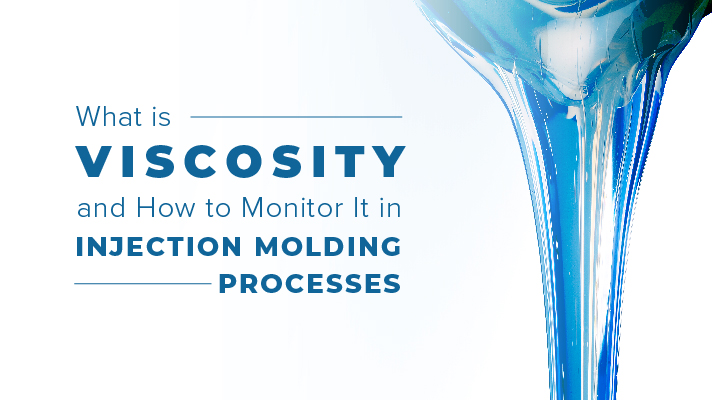
On the same shot, read the peak hydraulic pressure at the ram with the digital gauge. Fill into the mold and measure the time it takes from the start of injection to when transfer occurs. Set up any mold so you're transferring on forward screw position (go from fill to pack/hold based on the ram reaching a futed stroke position).ģ. Two-Shot Procedure for Testing the Machine's Load Sensitivityġ.
